Fuel Filtration & Mechanical Fuel Care Best Practices
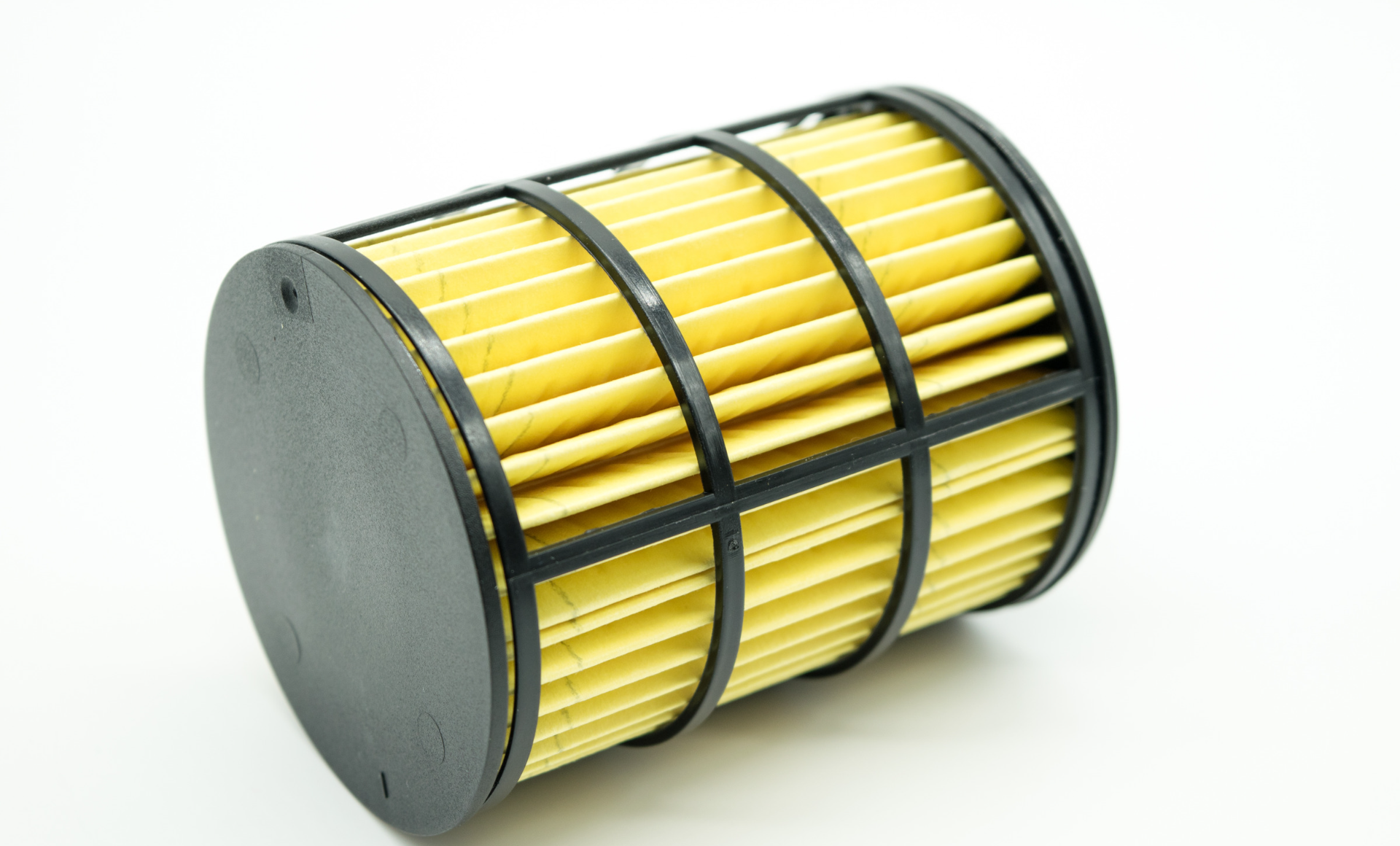
The Fuels Landscape Isn’t What It Used To Be
The fuels landscape is completely different than it used to be. Changes to the makeup of today's fuels, driven by stricter environmental regulations, have given us fuels that need more care than before. Advanced engine designs have evolved by necessity to meet more stringent emissions regulations. These advanced engines require a more advanced level of fuel cleanliness.
All of these changes, together, mean that fuel filtration are a bigger part of best practices of fuel management than ever before.
Emissions Regulations Drive Engine Design Changes Which Drive Changes in Fuels
Diesel engine designs are required to be more advanced than ever because of their key role in controlling emissions. Today’s diesel engines have modern design elements that require higher quality fuel and, in turn, higher quality filtration.
When we talk about emissions from burning diesel fuel, particulate matter and NOx are the two big ones. Today's diesel engine designs play a huge role in reducing those emissions, and they do it through elevated fuel injector pressures, multiple injections and controlled combustion temperatures in the engine.
In turn, the fuels these advanced engines use need to be cleaner than ever. Injector pressures have risen from 1000 bar in the 1980s to 2500 bar today and are projected to pass 3500 bar in the next few years. These increased pressures require small component clearances on the order to 2-5 microns, thereby placing a higher demand on fuel cleanliness.
Corresponding Changes In The Fuel Supply – ULSD and Biodiesel
Other changes on the engine side have created the need to change the nature of the actual fuels themselves. Meeting ever-stricter emissions regulations on NOx and PM (particulate matter) emissions can only be done through the use of advanced catalytic control systems. These control systems are expensive and must use sensitive catalysts to do what they need to do - catalystics that are easily damaged ("poisoned") if the wrong things are in the fuel.
To cut down on catalyst poisoning, the sulfur content of diesel fuel was reduced. Yet, removing the sulfur from diesel fuels changes the physical and physicochemical properties of the fuel.
- Naturally occurring lubricants are removed from the fuel along with the sulfur
- Distillation temperature and fuel oxidation stability, conductivity and aromatics are reduced
- Cetane number, wax content and cloud point are increased
What’s more, today’s fuels have a lot more biodiesel in them than they used to, and biodiesel fuel is less stable and more hygroscopic (water-attractive) than ULSD is. They have an increased intensity of fuel oxidation, causing premature fuel filter plugging and implying poorer storage stability.
"Fixing Fuel"
Chemical Treatments To Solve These Problems – They May Have Value But Limitations Must Be Recognized
Some in the industry pay lip service to all of these considerations and try to steer their clients, customers, and potential customers toward a one-size-fits-all chemical solution for the fuel.
- Water in your storage tank? Treat it with a chemical.
- Sludge in the fuel? There’s a chemical for that, too.
- Want to prevent problems with the fuel? You can do that, too - all you need is this fuel additive.
Informed fuel users and service providers can see right through this approach. People are tired of these kind of false or exaggerated half-truth claims overstating what can and cannot be done. People definitely don't want to feel like the advice they're being given is only there because they're being told what they want to hear (whether it's true or not).
Yes, there are legitimate and proven chemical solutions for specific problems that stored fuels may encounter or need to prevent.
Biocides are important, indeed, essential, for solving microbe problems that produce particulate and biomass in stored fuels.
Water controllers and other types of water treatments have their useful niche in keeping on top of tank water issues.
There are fuel stabilizers and sludge dispersants that can bring value to the table, too.
All this having been said, chemical "fuel additives" cannot do everything, despite what some fuel additive companies may tell you. Some of their most relevant limitations that should be considered are:
Water controllers can effectively control limited amounts of water but are not designed to make large quantities of water disappear. And the wrong kind of water controller cannot effectively deal with emulsified water in fuel.
Fuel stabilizers need to be added when the fuel is fresh, before signs of instability become apparent. They are appropriate for use in fresh fuel to keep its condition stable, but once fuel sludge has developed in fuel and its storage tank, a stabilizer will not put it back together again (and if something claims to do that, that's your sign to get far away from it).
Beyond Fuel Additives - Mechanical Fuel Processing
Since we know fuel additives have limits on what they can do, we should consider other things that can help us get where we need to be. Mechanical fuel treatment processes have a great deal of value in filling in the gaps to protect stored fuel quality. "Mechanical processes" are another name for fuel polishing.
Just as with our consideration of fuel additive treatment chemicals, we have to look at fuel polishing from the standpoint of recognizing the value it brings to the table, while not getting caught in overpromising ourselves by failing to remember its useful limitations in protecting ongoing stored fuel health.
Mechanical Fuel Processing – The Good
A good mechanical process for fuel will involve the use of filters and water separators to mechanically remove particulates and water from the fuel and its storage tank. This mechanical filtration is very useful for taking fuel that is out-of-spec on things like water and particulate content (i.e. fuel that fails the 500 ppm water/sediment specification) and bringing it back into specification – a great advantage for facilities that are legally required to keep their backup fuel ready for emergency use.
Mechanical processes are also the best way to handle the sizable amounts of water that many fuel storage tanks accumulate over time if they are not diligently watched (in other words, chemical fuel treatments have limits on the amount of water they can address).
The Need For Filtration To Remove Contaminants In Fuel
Mechanical processing and fuel filtration aren’t anything new. The need for filtration of diesel fuels goes all the way back to the 1930s or before, with a 1931 Caterpillar owner’s manual stating that 90% of diesel problems were due to dirt or water in diesel fuel.
Yet, filtration of the fuel is more difficult now than in the past because of an increase in organic contaminants present in diesel fuels. And yet it’s more important than ever. Today’s common rail fuel injection systems have critical filtration requirements due to increased operating pressures and tighter clearances for injectors and fuel pumps.
What’s Plugging Your Filters?
For contemporary fuels, there are three basic areas of concern – water, inorganic debris (sand, dust, rust), and organic debris (products of fuel breakdown, microbial products, and the waste products of fuel deterioration). This organic debris makes up the bulk of the contaminants normally found in fuel and fuel oil. Many times, people mistakenly refer to it as diesel fuel algae, when in fact, it has more to do with petroleum gums, varnishes, and lacquers than it has to do with "algae".
Filtration of today’s fuels is an essential step to remove the spectrum of contaminants in the fuel that may do harm to engines and equipment.
The Root Causes Of Filter Plugging
Filter plugging in storage tanks and vehicles is indicative that something is going on. But exactly what that is can be difficult to narrow down. In the wintertime, the answer is pretty easy - low temperatures cause wax crystallization in the fuel, leading to filter plugging. This is easy to prevent via the use of a cold flow improver or winter anti-gel treatment.
Outside of that, the fuel can have problems with particulate in the fuel and with water, which will need to be removed before they cause problems.
Organic Contaminants And Diesel Fuel
Filtration of the fuel is more important for today's fuel than in the past because of an increase in organic contaminants present in diesel fuels.
Organic contaminants in ultra-low sulfur diesel can damage elastomer fuel filter seals and shorten fuel filter life. In this case, the organic contaminants are the result of free radical reactions in the diesel fuel. These reactions are accelerated in ultra-low sulfur fuel due to the removal of naturally occurring antioxidants during the hydrotreating process for sulfur removal. As a result, a large number of peroxide molecules are generated. These peroxides promote oxidation and polymerization reactions and have a damaging effect on elastomer seals in fuel systems.
Particles In Fuel That Need To Be Removed
Fuel filtering, whether in storage or in the engine, is essential to remove the particulate and debris that can coat the walls and baffles of storage tanks, plug filters, clog fuel lines, and otherwise harm expensive components by their acidic nature.
The way the fuels of today have changed highlights their need for filtration more than ever. In the past, refineries used about 50% of a barrel of crude oil to make the distillate fuels (gas, diesel, natural gas) that are in highest demand. Today, through the use of refining techniques, that proportion approaches 90% or more. And this has severe consequences for the stability of those fuels and their tendency to form contaminants that need to be filtered.
Where Else Do These Contaminants Come From?
Not only are today’s fuel susceptible to formation of solids in storage as a result of their inherent instability, they can also be affected by particle contamination from other sources. These particles in fuel can be road dust, engine rust, wear particles or any other hard particles. Particle contamination gets into diesel fuel in multiple ways. The fuel itself can pick up particles during transit, even from gas pump to gas pump. Particles can also ingress through the tank vent. As the fuel tank is drawn down, ambient air is drawn into the tank, providing a source of particle contamination. Wear debris from fuel system components is another source.
ISO Ratings and Particles In Fuel
Typical fuel cleanliness levels are ISO rated at 22/21/18, which means a particle count of 20,000 – 40,000 per ml for particles of 4 microns or higher, 10,000 – 20,000 per ml for particles of 6 micron or higher, and 1,300 – 2,500 per ml for particles of 14 micron or higher.
Today (2014), diesel fuel pump manufacturers are requiring fuel with ISO cleanliness counts of 13/9/6 or better at the injector, with typical fuel cleanliness levels out of the pump measuring at 22/21/18. This difference represents a 1000 fold reduction in contamination between the fuel pump and the time the fuel reaches the injector system.
Today, particles significantly smaller than 4 µ in size are potential wear contributors to important parts. It is these particles that challenge the limits of fuel filtration ability.
Water In Fuel
Water found in diesel fuel can cause
- engine part corrosion and erosion,
- fuel lubricity deterioration,
- fuel pump capitation,
- fuel injector deposit buildup
- fuel filter plugging.
- It can also promote fuel instability and provide an environment where bacteria can grow.
Water can be found within fuel as free water, dissolved water, and emulsified water.
Dissolved water is dispersed in fuel molecule by molecule. Once the amount of water exceeds the maximum level for it to remain dissolved, water will fall out of the fuel and form a water in the fuel emulsion, with small water droplets suspended in the fuel.
The World Fuels Charter recommends a maximum water content in fuel of 200 ppm.
Water contamination can be introduced to the fuel system in a number of ways. Water can be transferred into the vehicles fuel tank as the level of dissolved water in the fuel equilibrates with the relative humidity of the surroundings. So at a minimum, some water is almost always introduced into the vehicle’s fuel system while fueling, though it may not necessarily be free water.
Water also enters fuel systems through tank vents, but unlike particle contamination, water is not necessarily driven by the level of fuel in the tank, but rather by fluctuations in environmental conditions like temperature and humidity.
Typical water contamination levels are able to fluctuate widely. Lab testing can show that a ULSD fuel can often have water saturation approaching 50 ppm at 50° and close to 200 ppm at 100°. This amounts to 1.7 ounces of water dissolved for every one hundred gallons of fuel. When fuel in the tank and airspace above it cool to 50°, the dissolved water holding capacity of the fuel is reduced to its starting value, iand the calculated amount of water is dropped out of solution and into the fuel tank as free or emulsified water.
In ultra low sulfur diesel, the loss of naturally occurring lubricants must be corrected with lubricity additives to protect the moving components of the engine that rely on fuel as a lubricant. These lubricity additives increase fuel surfactancy, which has an unintended effect of increasing the stability of water trapped in fuel. What this basically means is that adding of lubricity agents to diesel fuel makes it easier for water to become emulsified in that fuel.
Bio diesel fuel is inherently more hygroscopic than diesel fuel is.
Filtration Options For Water
Given the importance of removing these harmful contaminants, it’s a good idea to know something about the filtration options for this.
Water is generally removed from fuel using a stripping or coalescing filter mechanism. A coalescing filter separates water by allowing it to pass into the media where droplets are captured and combined to form larger droplets which are finally released on the downstream side. This is a standard option to remove free and non-emulsified water from fuel.
Emulsified water is a different story. As water droplets in low interfacial tension fuels form stable emulsions, both strippers and coalescers can become ineffective and cannot achieve required water filtration efficiency. In other words, it’s difficult for a water separator or coalescing filter to effectively remove emulsified water. When this is present, the best option is to treat the fuel with a demulsifier treatment, allow time for it to work, and then remove the accumulated free water.
For stored fuel users who lack the knowledge or confidence to do this, it may be a good option for them to talk to a service partner with experience in this.
Filtering Out Particulates and Filter Beta Ratings
To achieve effective particle filtration, it is important to use a filter with both a substantial-enough beta rating and a small enough absolute rating, to get the job done.
The Absolute rating speaks to the largest particle that can be expected to pass through the filter.
The Beta ratio is a quantitatively way to define how well the filter keeps particles from getting through. Beta ratios are defined as the ratio of the number of particles upstream to the number particles downstream at a specific particle size. This last part is important, as beta ratio or beta rating will always be given in conjunction with a particle size. Otherwise, it would not have enough useful meaning.
Fuel Filtration Systems In Vehicles/Engines
Vehicles and engines have their own filtration systems to protect the essential powerhouse from damaging fuel contamination. Effective fuel filtration in modern engines generally consists of 2 sequentially placed filters – a primary filter and a secondary filter. The primary filter usually has efficiency ratings from 7 µ 2/25 µ. Secondary fuel filters are placed between the transfer and high-pressure injection pump. The secondary filters protect the high-pressure fuel pump and sensitive fuel injection components from particles that can cause wear damage. Typical ratings for these secondary filters in high-pressure common rail fuel systems are in the 4 to 5 µ efficiency range.
All of this discussion about filtration speaks to the importance of good mechanical fuel treatment in maintaining the overall best health of stored fuels. The best fuel PM programs talk a multi-faceted approach to the use, grouping chemical treatments and mechanical processing and testing together to give them the most accurate picture of what the fuel is like in the present, what it may be like in the future, and what actually needs ot be done for the fuel (vs. what really does not).
Mechanical Processes For Stored Fuel Have Their Limitations, Too
The biggest limitations that fuel filtration and similar processes have in protecting stored fuel quality are that they do nothing to keep fuel problems from coming back. Fuel polishing removes from the fuel what’s not supposed to be there.
If you manage stored fuel of some type, you may even have had this scenario play out where you are. You engage the services of a fuel polisher, who may come out and do an admirable job of cleaning up darkened fuel and turning it clean and bright, just as it supposed to be. Yet, once the mechanical process is concluded, there’s nothing to stop the fuel from darkening again. Or developing a repeat microbe problem within a couple months. Mechanical fuel processing addresses current problems, it does not prevent future problems from happening.
The Role Of Fuel Polishers, Processors & Tank Cleaners
All of these considerations are especially pertinent to fuel polishers, tank cleaners, and fuel processors. They make it their business to keep fuel problems from impacting their customers. And that means that fuel problems impacting those customers also impact these fuel polishers and service providers, too.
Since fuel microbes are perhaps the biggest cause of fuel problems for virtually anyone who stores fuel, that also means they’re the biggest cause of headaches for fuel polishers. For fuel polishers and service providers to success in today’s fuel situation, they need to be able to help their customers deal with the fuel microbe issue that’s only going to get worse.
Top Ways Microbes Cause Fuel Headaches For Fuel Polishers
Microbes can negatively impact a fuel polisher’s reputation through customer dissatisfaction. If fuel or a storage tank has a microbe problem that isn’t diagnosed or doesn’t get fixed, it’s going to come back. That makes the fuel polisher look bad and creates tremendous customer dissatisfaction. After all, they paid good money for a fuel servicing job that, they assumed, was going to solve their problems. The fuel polisher subsequently gets blamed and their reputation gets hit. Not to mention the possibility of losing future business and the added costs of potential re servicing.
Microbes destroy fuel quality, which can undo the work that a fuel polisher does. Fuel polishers and services are brought in to turn visibly-poor quality fuel into pristine fuel that looks clean and bright. If there’s an undiagnosed microbe problem, it doesn’t take long for them to undo all the filtering and polishing and clean-up work the polisher did.
Microbes produce biomass in fuel storage tanks which plug filters that can shut down customer equipment or keep them from running during full load. The biomass produced by microbial infestations cause the same fuel problems that excess particulates and sludge content will. This is an obvious problem for fuel polishing customers when it comes time for them to use the fuel.
Microbial presence and its effect on fuel can create uncertainty in the customer’s mind about whether their fuel will perform, which then can make them doubt the quality of the fuel polisher’s service. When an undiagnosed microbe problem is allowed to fester and develop, it creates doubt in the customer’s mind. They weren’t expecting to have microbes problems after having service work done by someone that (they thought) had a handle on things. Fuel polishing is such a competitive business, no fuel polisher can really afford to lose the confidence of their customers.
Microbes in fuel can often be misdiagnosed as other problems. This is where knowing what one is doing can set one party apart from another. Given that microbes can be linked to some many different types of problems – excess particulate, fuel instability, free water in the tank – if the expertise or knowledge isn’t there, the underlying cause (microbes) can be missed in favor of solving these more superficial symptoms. In other words, the forest can be missed for the trees. The real cause of the problem (microbial infestation) is missed while the fuel polisher is busy taking care of the problem (like water and sediment content) that was caused by (or helped to contribute to) the microbe problem.
This kind of misdiagnosis leads to ineffective service that doesn’t address the real problem. That increases the chances for future problems like the ones we were just talking about above.
Microbes can resist incorrect treatments, causing wasted time and money. This is another way of saying that if fuel polishers don’t diagnose correctly that a microbe problem is present, then their service work may clean the fuel up temporarily but it’s not going to last. The microbes will continue to do their "dirty work" and the service time and money will end up being wasted.
You may argue "no it’s not; the fuel looks clean and bright now. Problem solved." Perhaps, but that ignore the fact that the customer is expecting zero problems to come back. If a microbe problem isn’t solved, they’re going to have a repeat problem, and it’s going to be sooner, rather than later.
Helpful Resources
Managing Fuel in 2018
Webinar
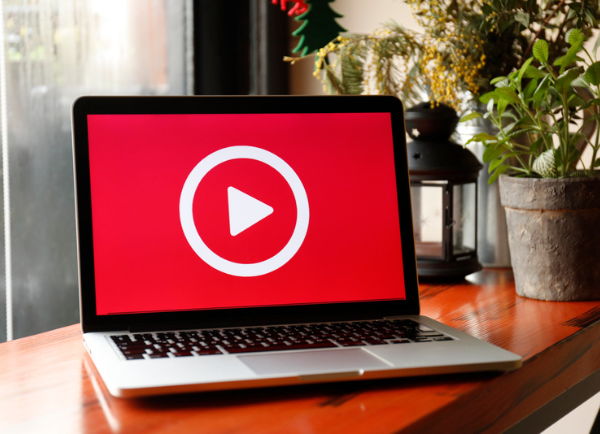
How to Prevent Diesel Fuel Fungus
Technical Sheet
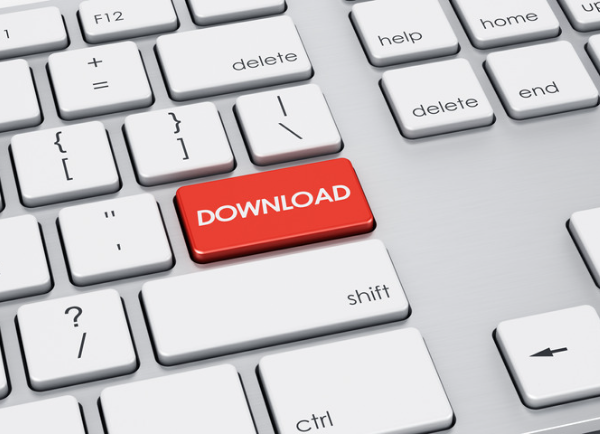
Could Half An Approach Be A 100% Mistake
Tip Sheet
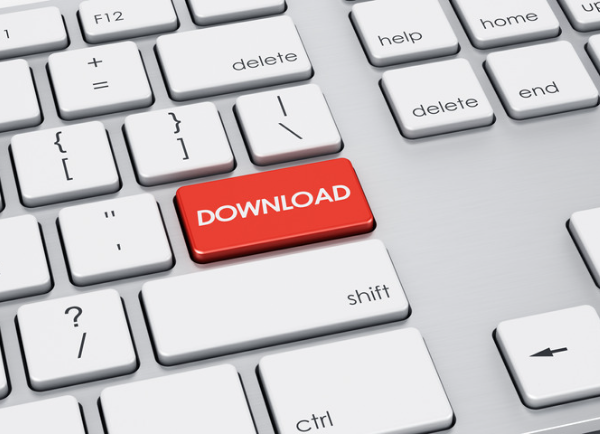
Fuel Tank Contamination Checklist
Checklist
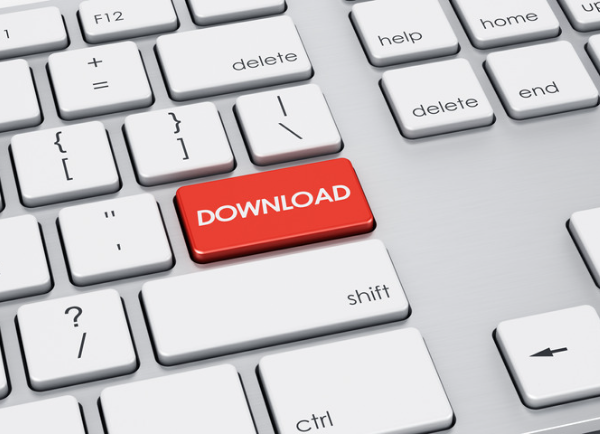
Fuels Aren't What They Used to Be
Whitepaper
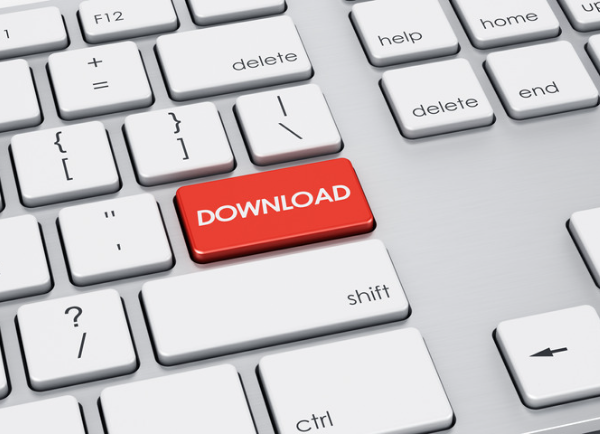
The Essential Fuel Tests That Fuel Polishers Need to Know About
Whitepaper
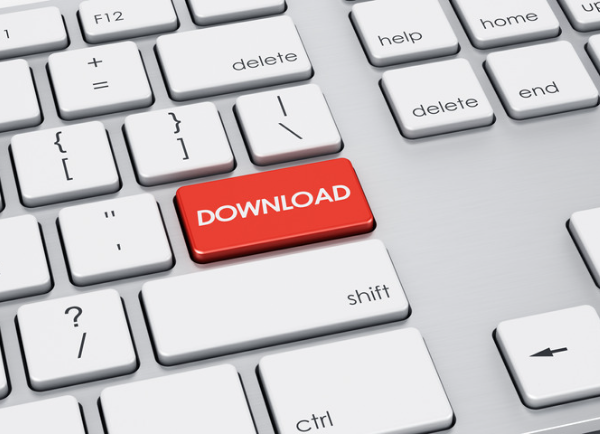
Fuel Changes and How They Affect You
Webinar
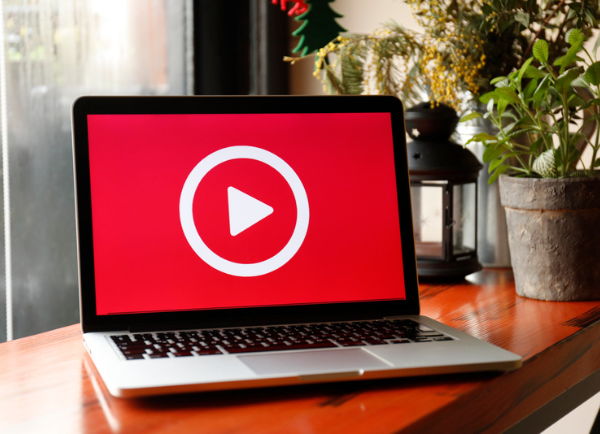
What's My Fuel Health Score?
Webinar
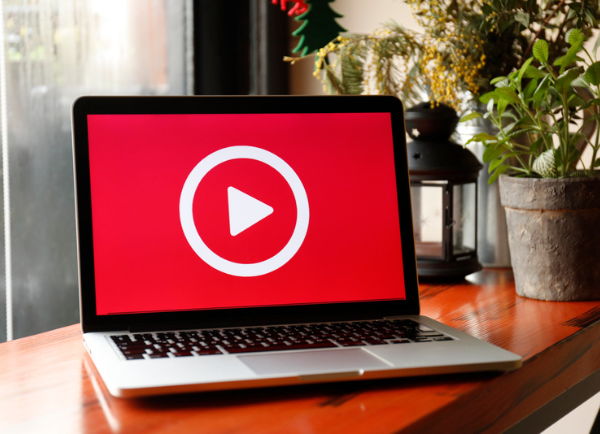
Fuel Checklist for Stored Fuels
Checklist
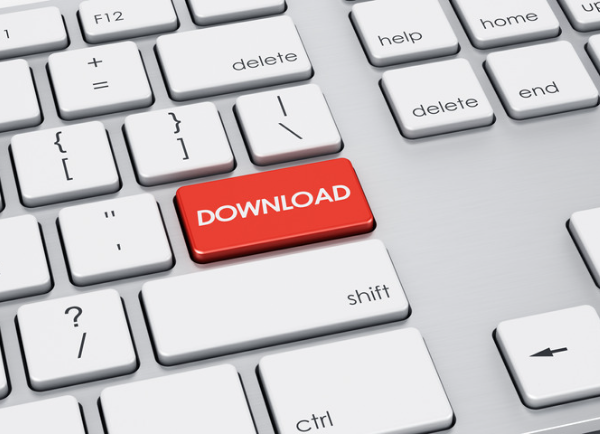
Fuel Filtration on our Commercial Blog
3 min read
Today's High Performance Fuel Filters: Historically Good
Apr 25, 2024 by Erik Bjornstad
4 min read
Diesel Filtration: How Effective?
Sep 6, 2017 by Erik Bjornstad