Fuel Maintenance: What's, Why's & How's
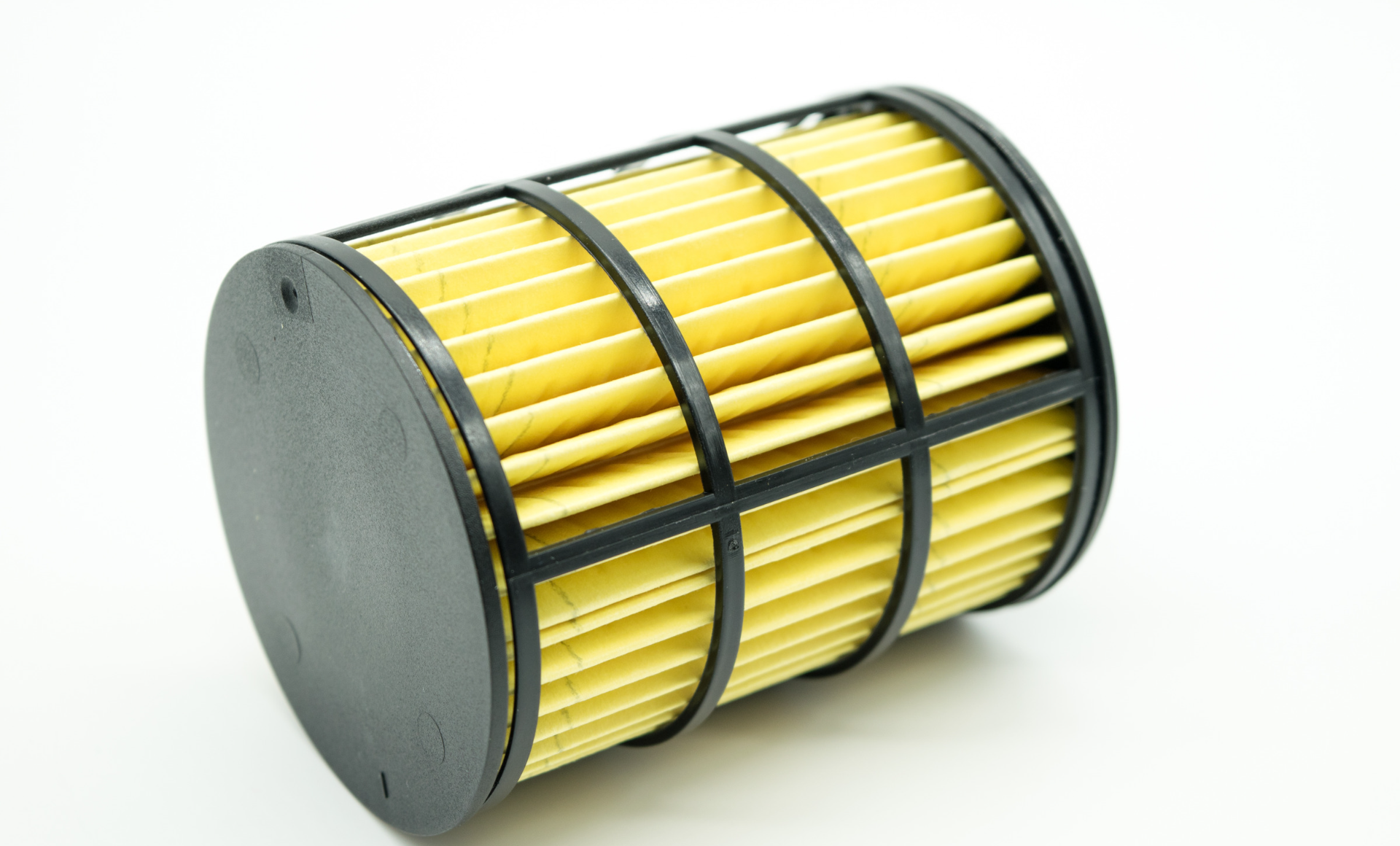
If there’s one thing you can count on in life, it’s that things change. That’s especially true of fuel. Today’s fuel is not the same stuff they used 20 or 30 years ago, and that means you have to treat it differently. It has different problems that need to be handled differently. Fuel maintenance for today’s diesel fuel is a whole new ballgame.
Ensuring Stored Fuel Quality
Quality maintenance of emergency stored fuel is crucial for proper combustion, reduced emissions, and engine efficiency. When disaster strikes, relying on emergency fuels is essential. The readiness of the stored fuel is what determines the proper functioning of mission-critical generators, vehicles, and equipment.
Whether you're dealing with hurricanes in Florida or tornadoes in the Midwest, these fuels power your critical operations. Ensuring they perform seamlessly is paramount to effective emergency response.
The same expectations apply for stored fuels powering essential vehicles and equipment in non-emergency situations. The expectation is that these fuels will function like they’re supposed to. The expectation is *not* that generators on their monthly load-test will sputter and shut down at only 50% load. Whatever kind of fuel you use, in whatever capacity you use it, there are best practice things that you as a fuel manager can do to ensure that your stored fuel is going to continue to be ready to use when you need it the most.
How Fuels Have Changed
The fuels of today have changed in response to the needs of the consumer and the needs of the machines that use them. New discoveries and technologies have forced fuels to adjust to keep meeting the needs of the market. The engines of today are much different than the engines of the 19th and first half of the 20th century. Over time, however, both diesel and gasoline have changed, through things like introduction and then removal of TEL, added detergency in gasoline, the removal of sulfur and aromatic limits in diesel, and the introduction of biofuels like ethanol and biodiesel to the nation’s fuel supply. Not to mention use of cracking processes as the refinery.
The World Has Changed
In the past, a book titled "The World Is Flat" highlighted the increasing global connectivity and the rapid resource consumption of developing nations. By 2012, the International Energy Agency revealed a significant shift: oil consumption in developing countries surpassed that in developed nations. At the turn of the century, developing countries consumed 70% of the oil used by developed ones. However, this balance has changed due to booming populations in countries like China, India, Southeast Asia, and Brazil, resulting in greater demand for resources from parts of the world that never demanded it before.
Meeting this demand has proven challenging as the ability to refine crude oil struggles to keep pace. While the number of refineries has decreased, their efficiency has improved. In 1982, the US had 301 refineries with a capacity of 17 million barrels per day. By 2013, this number had reduced to 139 refineries, maintaining the same capacity to meet the demand.
Fuel stability during storage has also shifted over time. A 1960s study by the US Army found that gasoline could be stored for 2-5 years, and diesel for over a decade without issue. Today, these numbers have plummeted, with common gasoline (E10) having a shelf life of around 90 days. Diesel Fuel #2 experiences a 26% degradation in the first 28 days, escalating to 95% with water content. The reliability of fuel storage has drastically declined.
Squeezing More Fuel From Each Barrel
The dynamics of the fuel industry have shifted. Demand for petroleum is soaring, but refining capacity hasn't kept up.
To meet demand, refineries use advanced processes to extract more gasoline and diesel from each barrel of crude oil, leading to increased yields. These processes, known as cracking, break down larger molecules in crude oil, converting them into smaller, more valuable molecules for fuels.
However, a downside emerges – these smaller molecules with double bonds are highly reactive and lead to faster degradation of gasoline and diesel. This results in the rapid formation of sludge, varnish, and particulates, diminishing fuel stability.
Fuel Changes To Be Greener
The increasing move towards greener policies have also changed the fuels we use. Consumer demand has translated into executive action that has impacted the fuels we use today. The Clean Air Act of 1992 was the key fulcrum when we talk about laws that spurred changes to our fuels with the goal of having a cleaner environment.
Virtually all on-road gasoline we buy in the United States has at least 10% ethanol content in it, and the blending of up to 5% biodiesel content into diesel fuel is now common practice across the country. This means virtually every diesel fuel user has been using biodiesel, whether they realize it or not. While biodiesel fuels have some positive attributes (high lubricity, renewable fuel), their inclusion in the diesel fuel supply does not help with fuel stability problems. To make a long story short, even low levels of biodiesel content increases microbial problems in stored fuel because microbes love to feast on it. In addition, biodiesel is hygroscopic, which means even low levels of biodiesel content can accelerate water accumulation in storage tanks.
The indelible fact that stored fuels are different from how they used to be should lead us to seriously consider that we need to rethink how we take care of stored fuel. We need to reconsider the issue of fuel maintenance.
Removal of sulfur to create ULSD
Diesel fuel has undergone significant changes in its sulfur content over the years. Traditionally, on-road #2 diesel contained up to 5000 ppm of sulfur. However, environmental concerns prompted Congress to take action in 1990, leading to a reduction in sulfur emissions to combat issues like acid rain and urban air pollution. This resulted in a 90% reduction in on-road diesel sulfur content by 1993, creating Low Sulfur Diesel (LSD). Further reductions led to Ultra Low Sulfur Diesel (ULSD) with a sulfur cap of 15 ppm in 2006. This remarkable reduction of 99.7% has greatly benefited the environment and improved diesel engines' cleanliness by around 99%.
The process to remove sulfur from diesel involves hydrodesulfurization at refineries, resulting in ULSD with a sulfur content of 4-7 ppm. While achieving its environmental goals, this refining process also slightly decreases energy content, leading to a minor decrease in peak power and fuel economy. However, overall, the move toward cleaner diesel has been effective in achieving its intended objectives.
What Are The Problems With Today’s Fuels?
We’ve alluded to some of the fundamental changes to today’s fuels, but what fuel problems have these changes led to and how are they linked? From this point on, virtually all of the discussion will center on stored diesel fuel. Stored gasoline is a discussion for another day.
Today’s diesel engines are more sensitive
The big elephant in the room here is how diesel engines have changed dramatically. These design changes of diesel engines are aimed at controlling emissions. Today’s diesel engines have design elements that require higher quality fuel and, in turn, have much lower tolerance for the kind of contamination that can show up in stored fuels if it’s not properly maintained. They achieve much lower particulate matter (PM) and NOx emissions through elevated fuel injector pressures, multiple injections and controlled combustion temperatures in the engine. Injector pressures have risen from 1000 bar in the 1980s to 2500 bar today, and are projected to pass 3500 bar in the next few years. These increased pressures require small component clearances on the order to 2-5 microns, thereby placing a higher demand on fuel cleanliness.
Sludge and Organic Contaminant Buildup in Stored Fuels
This happens because as the fuel is forming these heavy polymers, they drop out and collect at the bottom of the tank, resulting in a sludge buildup in the storage tank itself. This is a problem because, first, sludge like this represents energy value that’s not contributing when the fuel is burned. And second, sludge can plug filters and contribute to engine deposits if it happens to be consumed by another piece of equipment.
Organic contaminants in ultra low sulfur diesel can damage elastomer fuel filter seals and shorten fuel filter life. In this case, the organic contaminants are the result of free radical reactions in the diesel fuel. These reactions are accelerated in ultra low sulfur fuel due to the removal of naturally occurring antioxidants during the hydrotreating process for sulfur removal. As a result, a large number of peroxide molecules are generated. These peroxides promote oxidation and polymerization reactions and have a damaging effect on elastomer seals in fuel systems.
The Effects Of These Fuels In Today's Engines
For the reasons explained above, today’s diesel fuels don’t burn as cleanly or completely in an engine.
So you don’t get the full energy value out of them, and b) you get soot particles and black smoke left over. Injector deposits happens because you’ve got gums and varnishes that have already formed in the fuel, they don’t really atomize well, instead they cook in the injector pintle. And this is important because, for a vehicle, injector deposits are the single biggest factor in influencing mileage, apart from driver behavior Lastly, you get shortened DPF filter life because there’s more unburned fuel and soot being produced to fill the unit up faster and shorten the regen intervals.
Black smoke
Because these unstable heavy components don’t burn as seamlessly as fresh fuel, the combustion of the fuel will produce black smoke and higher levels of partially-burned particulate matter.
Less Resistance to Microbes
Lower fuel energy content isn’t what people are too concerned about in this case. Today’s ULSD is much more prone to microbial problems because of these changes. It’s the one with the potential to cause the most problems of all the effects discussed so far.
Regardless of ULSD, microbial presence in fuel tanks is one of the biggest and most universal problems faced by stored fuel users today. The microbes get into the tank from the environment (such as in the air that circulates in the tank, or attached to dust particles), or attached to water vapor. You can’t keep them out. They grow and multiply at the interface between the water later and the fuel layer, and they draw what they need to multiply from both layers. Microbial growth is possible anywhere free water layer is present in a tank
How do tanks build up water? Most storage tanks collect water over time over simple atmospheric condensation – temperature changes between day and night. Or they can get water in them from other sources, such as fuel drops, tank leaks, or even “ingress” with an underground tank that has a spill bucket that fills up with rain water. That stuff happens more often than you think. If you could keep all water out of a storage tank all the time, then it would be fairly easy to control microbial growth. But in real life, it’s next to impossible to do that.
Fuel Microbes Linked To Problems Of Filter Plugging & Easy Spread
Microbes grow in the fuel tank, multiply, and produce biomass and slime growths which will plug filters in the storage tank. So, if you’re a fuel or tank manager and you notice an increase in the rate of filter changes needed, that’s one sign you need to look closer at what’s happening in your tank.
But this isn’t the only thing to be concerned about. The problem is easily spread to vehicles and other tanks through fuel transfer. That’s another reason why it’s important to deal with the problem when you find it. If it spreads to things like vehicles and equipment, filter plugging issue becomes a real problem because this shuts down the vehicle or engine, which takes the machine out of commission, and depending on what you need it to do, an extra added expense and headache.
Microbes Linked To Fuel Instability
Microbes are heavily linked to accelerated breakdown of fuel stability because, not only do they produce biomass, but they give off acids and biological byproducts that attack and break down fuel quality. This causes the same problems that we saw as we talked about fuel instability from cracked feedstocks - engine deposits, black smoke and emissions, and rough, inefficient engine operation This last problem is the biggest concern, perhaps, for critical use system.
Microbial Fuel Instability Is A Critical Use Problem
Critical use systems and emergency management systems – they’re different from fleets and those kind of users - they store fuel because it’s intended to be used in an emergency. There’s a high value placed on that stored fuel performing properly when it needs to. Because of the nature of these things, you can’t predict when that’s going to be. Emergency backup systems aren’t like fleets which have predictability in fuel usage. And that makes it more likely that, unless there are rules in place that force users to check and/or test fuel at given specific intervals, it’s very likely that this kind of emergency backup fuel may not have been checked in a while. Out of sight, out of mind. And that can lead to unfortunate situations like we’ve seen in the recent past.
When the fuel quality is degraded, it increases the chance of system failure and engine shutdown at critical times when it can least be afforded. This has been seen in the past, during Katrina, Sandy, and after the 2005-2006 hurricane blitz across the Southeast. Users in all of these times had emergency generators that would not start, or they tested the generators afterwards and found widespread system failures because the fuel quality had been destroyed by microbial growth in the tanks. And they didn’t even know it until it was too late. These ended up being huge costs, just as a result of microbes in stored fuel.
Microbe-Related Corrosion Damage In Tanks
Speaking of microbes, the last major problem we see centers on microbial presence in fuel systems over a long period of time being strongly associated with corrosion damage in storage tanks. Called microbially-influenced corrosion or MIC. Microbes cause MIC because their biological activities result in the production of acid byproducts that attack tank surfaces. Some kinds of bacteria have been known to perforate a 5mm thickness of 316 steel in little more than one month. This may be a rather extreme case, but it does serve to illustrate that microbial corrosion can cause serious damage in shorter time than you might think. this damage is expensive and needs to be repaired when it happens, often running into the thousands per tank. If you’re in charge of purchasing or maintaining storage tanks, you know the scale of expense that we’re talking about.
How do ULSD changes lead to microbe problems?
So how do ULSD changes lead to these microbe problems? Few anticipated the explosion in microbial growth in storage tanks filled with ULSD. Turns out, there are two qualities of ULSD that directly contribute to them. ULSD is more hygroscopic than other diesel, meaning it attracts more water, which is exactly what microbes need. Second, removing the sulfur removed something that helped limit microbial growth. Microbes do not particularly like to be around it. Also, the same regulations that limit sulfur content also call for reduced aromatic content. This also causes microbes to flourish because removing aromatics leaves a greater proportion of things that the microbes like to use as food sources. So, removing the sulfur and aromatics from the fuel removed much of what prevents microbes from readily growing in storage tanks.
Water in Fuel
Really, we should have mentioned water before we talked about microbes, given how the two problems is so strongly linked. Water in stored fuel not only helps microbes thrive, it contributes to a host of serious problems.
- Engine part corrosion and erosion,
- Fuel lubricity deterioration,
- Fuel pump capitation,
- Fuel injector deposit buildup
- Fuel filter plugging
It can also promote fuel instability and, of course, provide an environment where microbes can grow.
Water can be found within fuel as free water, dissolved water, and emulsified water. Dissolved water is dispersed in fuel molecule by molecule. Once the amount of water exceeds the maximum level for it to remain dissolved, water will fall out of the fuel and form a water-fuel emulsion, with small water droplets suspended in the fuel. As the amount of water grows beyond this, it will coalesce and collect as a free water layer.
Typical water contamination levels are able to fluctuate widely. Lab testing can show that a ULSD fuel can often have water saturation approaching 50 ppm at 50° and close to 200 ppm at 100°. This amounts to 1.7 ounces of water dissolved for every one hundred gallons of fuel. When fuel in the tank and airspace above it cool to 50°, the dissolved water holding capacity of the fuel is reduced to its starting value, and the calculated amount of water is dropped out of solution and into the fuel tank as free or emulsified water.
Where does the water come from? Water contamination can be introduced to the fuel system to the same basic paths as particle contamination. Water can be transferred into the vehicles fuel tank as the level of dissolved water in the fuel equilibrates with the relative humidity of the surroundings. So at a minimum, some water is almost always introduced into the vehicle’s fuel system while fueling.
Water also enters fuel systems through tank vents, but unlike particle contamination, water is not necessarily driven by the level of fuel in the tank, but rather by fluctuations in environmental conditions like temperature and humidity.
In addition, in ultra low sulfur diesel, the loss of naturally occurring lubricants must be compensated with lubricity additives to protect the moving components of the engine that rely on fuel as a lubricant. These lubricity additives increase fuel surfactancy, which has an unintended effect of increasing the stability of water trapped in fuel. What this basically means is that adding of lubricity agents to diesel fuel makes it easier for water to become emulsified in that fuel.
Unintended Consequences: Unreliable System Operation
It’s one thing for a diesel truck to have injector deposits and more mileage. It’s a different, higher level of concern when you have stored diesel fuel for an emergency backup system for a place like a hospital. That stored fuel is eventually called upon to work in a critical situation. If the fuel is unstable, if it has broken apart, it’s not going to burn efficiently in the generator or machinery. And this presents potential issues for critical use applications.
The 2003 Blackout - hit a large part of the country and affected 50 million people. Fully 20% of emergency systems put into place specifically to provide power in such an emergency failed to work because the fuel contained therein didn’t work.
Superstorm Sandy (2012) – the well-publicized case of NYU’s Langone Medical Center and Bellevue Hospital having to evacuate critical care patients because their back-up generator systems failed.
Hurricane Katrina – when 80% of New Orleans wasn’t being flooded by 20 feet of water, a significant number of backup generators simply failed to work, due to lax maintenance.
Fuels and Operations professionals like to think they’re adequately prepared for these kind of situations. But there are factors that might prove these assumptions aren’t as solid as they think:
TIME - It’s clear that you don’t get much warning with hurricanes, which is why they can catch even the best fuel administrators off-guard. The State of Florida estimated that a 12-hour notice is the best advance that people can expect. This is a troubling contrast to the fact that, even in a prepared state like Florida, some areas take 28 hours or more to execute essential response tasks like evacuations.
FREQUENCY – Trends and records of past storms show that most coastal states can expect to be exposed to a hurricane at least once every 25 years. And we all know what happened in 2004 and 2005.
LACK OF REAL PREPARATION – Over 80% of U.S. localities have a formal disaster plan on-hand. But an audit by the International City Management Association concluded that local governments continue to be surprised (by storms) despite this fact, yet often fail to improve their preparation plans even after a disaster has been experienced in their area. Why do they fail when they should know better? Most likely, it’s due to a combination of a lack of relevant experience with the issue of disaster response, failure to learn from experience, lack of commitment to doing the work (which may not always have an immediate and visible payoff), and lastly, doing the wrong kind of planning (which may target the wrong areas).
Summarizing The Problems
If your engine or generator isn’t running the way it should, it’s going to be due to either the fuel not meeting specifications or the engine not burning the fuel in the way it was designed to. The most common problems seen in the fuels supplied to applications like yours can be traced to five root problems.
Fuel-Related Problem |
How this occurs |
Water in fuel |
Fuel storage systems inevitably accumulate water through condensation from ambient air, if not from breaches of the mechanical integrity of the system (i.e. rain water leaks). |
Microbes in fuel |
Microbial colonies feed off petroleum fuels and accumulated water to multiply and thrive within storage tanks. |
Fuel instability |
Exposure to oxygen, water, heat, light and certain metals causes chemical chain reactions in the fuel that degrade its quality in storage. |
Low cetane value |
The value of fuel cetane value is relative to the requirement of the diesel engine. |
Tank sludge buildup |
Sludge forms from the separation of heavier petroleum components in stored fuel dropping out of solution and settling to the bottom of the storage tank. |
The great majority of operational problems with engines and systems today can be traced to one or more of these fuel-related issues. Hence, solving these problems will alleviate many of the subsequent symptoms, saving the user time and money.
Here’s another way to look at this. Which of these causes are really responsible for the fuel problems you’re experiencing? As some of these problems can share multiple symptoms in common, narrowing them down can be difficult. To help, we create this handy checklist of common fuel symptoms, matched to their most likely causes.
Symptom |
Water in fuel |
Microbes in fuel |
Fuel instability |
Low cetane value |
Tank sludge buildup |
Excessive filter plugging |
![]() |
![]() |
![]() |
|
![]() |
Water phase detected (see notes) |
![]() |
![]() |
![]() |
|
|
Darkened fuel |
|
![]() |
![]() |
|
![]() |
Poor/noisy diesel engine running |
|
|
|
![]() |
|
Lack of power |
|
|
|
![]() |
|
Injector damage |
![]() |
|
|
|
|
Tank corrosion evidence |
![]() |
![]() |
|
|
|
Higher emissions & black smoke |
|
|
![]() |
![]() |
![]() |
Tieing All of This Together: The Need for Better Fuel Maintenance
Let us take a step back and consider the number of old fuel storage tanks out there. Many with trace amounts of old fuel in them, and many having had ULSD added to them. The Southeast hasn’t had a really active hurricane season since about 2004-5. So there are a lot of emergency fuel storage tanks that haven’t had much attention paid to them. The fuel is in there for future emergencies, but it’s just sitting there. Consider also that that hurricane season happened right before the implementation of ULSD. Many of these tanks have had ULSD added to them, but nobody’s really checking on them.
What do you think’s going to happen with those tanks and the fuel if we get another hurricane blitz some time? They’ll go to use the fuel and find some serious problems. The smart people, the smart businesses, they’re going to recognize the possible problem and take action before it’s too late. They’re going to recognize that they need to take fuel maintenance more seriously.
The Best Elements of Fuel Maintenance
Best practice fuel maintenance consists of a three-pronged approach – chemical, mechanical and testing. Testing is always mentioned last, but we should really talk about it first.
Many professionals don’t want to admit that they need a multi-faceted approach to fuel upkeep. Fuel polishers are experts in mechanical processing and remediation of the fuel. Fuel additive companies are experts (well, at least some of them anyway) at chemical treatments to solve or fix fuel problems. You’ve heard the saying to a man with a hammer, everything is a nail. These groups tend to want people to believe that their business is the only thing needed to solve any and all fuel problems. We know that’s not even close to being the case. The most complete and best solution for fuel maintenance often involves both things – mechanical remediation and chemical treatment, along with testing to measure results.
Testing and monitoring
Testing and monitoring is really where it all starts. And yet, it’s the part that is most ignored by the most people, including those who should know better. Why should this be the case? Monitoring allows you to keep track of the condition of the fuel over a period of time. Testing allows you to document the actual condition of the fuel. It just seems logical that you would need to have this kind of information in order to know what you need to do with the fuel. Or even if you need to take any action at all.
How do you know what needs to be done? How do you know when action needs to be taken? You know this by practicing fuel testing and monitoring of its condition. Proper fuel maintenance practices never ignore this.
Monitoring: Have you checked your tank(s) lately?
For many who are not subject to regulations that force them to take action, fuel storage tanks may go years without being looked into. And while those tanks are sitting there, problems with water and sludge and microbes are growing inside. The longer they stay undetected, the worse the consequences.
It's important to also incorporate periodic fuel testing among the recommended best practices of protecting stored fuel quality. Fuel testing gives an essential diagnostic picture of the condition of the fuel, without which, it is much more difficult to compile an accurate picture of how healthy the stored fuel is and to know which specific fuel quality problems need the most attention.
The idea of fuel testing can be, for many fuels professions, both daunting and confusing. Unless they’re under the directives of specific testing requirements by a regulatory agency, it may be difficult to know which of the many tests for stored fuel are good ideas and which are not needed. It is not difficult at all to throw money away on tests that don’t mean what we think they mean, if you don’t know which ones are really needed and which are not.
Check tanks for water and sludge at least quarterly. Use water paste and a tank stick to gauge water depth in storage tanks. If you don’t want to do it yourself, contract out with a qualified group who can do it for you.
Testing: When’s the last time your fuel was tested?
Just as with storage tanks, you may already be subject to requirements to do fuel testing at given intervals. Hospitals and critical use facilities typically fall under these requirements. For everyone else, the most common stance is a reactive one – if you don’t see problems in the present tense, everything is fine. You’ll deal with problems if you come across them. On the other hand, fuel sampling, even if it’s just once a year, goes a long way in identifying future problems and heading them off.
Without fuel testing, you have no sure way of knowing these critical problems exist.
Sample the fuel in each storage tank for testing at least once a year.
There are only a small number of tests that you need to pay attention to - the tests that tend to be required for critical use installations, meaning they are considered most relevant to ensuring that stored fuel will perform properly in essential situations
Where to have tests like these done? There are plenty of testing laboratories available that can do these tests with a pretty quick turnaround. You should seek to establish relationships with a service provider company that has existing relationships with certified labs. Many times, such a partner can get the same tests done at a fraction of the normal “a la carte” cost you would have paid, and the company will also take care of packaging up the sample, submitting it for testing, and apprising you of the results.
What to expect if the fuel is bad?
Critical use facilities have certain specific fuel tests specified for them because there can be disastrous consequences if the fuel fails one or more of these specs while being called upon to perform in an emergency. Here are some of the most common ones:
Essential Test #1: Distillation |
A test that measures the combustion properties of the stored fuel and ensures the fuel burns properly in the engine. |
If the distillation curve of the stored fuel is off, the engine will run roughly, make black smoke, or may not even start at all.
Essential Test #2: Sulfur Content |
Measure the sulfur content to ensure it does not exceed the legal limit. Off-road diesel used to be exempted from the 15 ppm sulfur cap applied to on-road fuel. That exemption has been phased out. Which means everyone, including municipalities and stored fuel professionals, will need to be monitoring the sulfur content of their stored fuel. |
If the sulfur content is too high, it puts you at risk for violating environmental laws.
Essential Test #3: Water & Sediment |
A test that documents the level of free water and sediment present in a fuel sample. Excessive levels of either one indicates the fuel is unstable and also prone to microbial contamination. |
If the Water & Sediment test fails, the fuel is probably unstable and may not be useable. It will burn poorly in the engine, and create black smoke and harmful deposits in the engine and injectors.
The water accumulation danger becomes compounded when you add water accumulation in storage tanks, resulting in the perfect recipe for the destruction of stored fuel quality. Water plays several roles in the destruction of stored fuel quality. The accumulated water builds up in fuel storage tanks that are vented to the outside. Temperature changes from day to night cause condensation to develop on the inside of the storage tanks; this condensed water rolls down the sides of the tank and sinks to the bottom of the diesel fuel, because water is heavier than diesel fuel.
Every fuel management professional knows it is common to find at least some water sitting at the bottom of every storage tank. This water enhances the possibility of microbial growth in that storage tank. Bacteria, fungi and microbes need a small layer of water interfacing with a layer of diesel fuel in order to get all the things that they need to grow and thrive inside of a fuel storage tank. Any time you have a layer of water in a storage tank, you have the enhanced potential for microbe growth and problems. Another factor water plays with respect to stored fuel quality is its role in the chemical breakdown of the diesel fuel. Diesel fuel can undergo chemical breakdown over time by a number of avenues. Microbes that infest storage tanks produce acids and corrosive substances as a result of their biological processes. These biological byproducts accelerate the breakdown of the quality of the diesel fuel just as you would expect an acid to do. They’re also strongly associated with corrosion damage of storage tanks themselves.
Most fuel storage professionals have a protocol to control water in tanks. There are water coalescers, filters and centrifuges that can allow for the removal of significant amounts of water from tanks. There are also highly effective fuel treatment options that will absorb significant amounts of water and cause it to be locked into the diesel fuel for combustion. Water removal is also an essential element of a quality fuel & tank service program that typically involves removal of excess water in storage tanks coupled with the addition of both water controllers and biocide treatments to stop microbial problems before they start.
Essential Test #4: Cetane Index |
Measures the “combustion quality” of diesel fuel. Having the right cetane rating in diesel fuel is essential for any diesel engine to run properly at starting and in cold weather. |
Inadequate cetane rating has significant effects on the running of the engine – rough and noisy operation, higher instances of black smoke. It also makes a diesel engine difficult to start, which is a death sentence for emergency generators and critical-use systems.
Essential Test #5: Fuel Stability
No matter if you use fuel in an emergency vehicle or heavy duty equipment or a backup generator, if the fuel quality is not within specification, then the vehicle or engine is not going to run properly or it may not even run at all when it is needed most. This fuel quality deficit is really caused by what ends up in the fuel that does not burn as well as the fuel itself. When you hear about fuel oxidation, gums, varnishes and fuel sludge, these are parts of the diesel fuel mixture that used to be soluble and in solution with the fuel blend, but which have undergone chemical reactions (with other unstable fuel agents) to form substances that are heavy enough to fall out as sludge. These substances don’t burn very well when they are used by the engine.
Biodiesel and regular diesel fuels are prone to what is known as oxidative stability breakdown. Water, oxygen, light or heat, and bacterial byproducts – all can be shown to chemically deteriorate and break apart diesel fuel and biodiesel blends. They all contribute to either providing the fundamental ingredients for the chemical reactions that causes a fuel’s break down, or the acceleration of the oxidative breakdown of the fuel quality over time.
Exposure to water and oxygen in the air provide oxygen that is the essential ingredient in oxidation and hydrolysis chemical reactions. These are the chemical reactions that attack diesel fuel molecules, break them apart and turn them from stable molecules to unstable molecules that want to form sludge and deposits in stored fuel. Biological byproducts of bacteria and fungus in fuel tanks also lead to tank corrosion and the breakdown of stored fuel in the tank because of their acidic nature. Exposure to heat provides the energy catalyst needed to make sure that these harmful chemical reactions actually happen at a faster rate in the fuel.
The marketplace offers different solutions to help with fuel stability deficits. Fuel stability treatments are preventive treatments that aim to keep these substances from forming, instead keeping the fuel mix together so it burns as well as it is supposed to. Fuel “polishing” is a reactive (but sometimes necessary) mechanical step that provides value by removing existing sludge and asphaltene dropout from the fuel so that the fuel burns as it’s supposed to. Both of these steps offer value points to the fuels professional worth considering, especially as part of a fuel preventive maintenance (fuel PM) program.
Monitoring: Have You Checked For Microbes?
If you have microbes in your fuel tank, it’s inevitable that you’ll have big problems sooner rather than later. Fuel that’s been sitting around for years, such as in limited-use backup generators, is virtually guaranteed to have significant microbial growth in those little-used storage tanks.
Microbial growth in fuel storage tanks is the single biggest cause of fuel problems and destroyed fuel quality. They plug filters, change the pH of stored fuel, and cause damaging tank corrosion. Any time you have water present in a storage tank, microbial growth isn’t far behind.
So it’s important to check for and monitor microbe levels in fuel storage tanks, at least once a month. There are dipslide options that give you a pass/fail indicator of microbial presence. However, we find that ATP testing is far more preferable, as it gives you an actual number of microbes present in fuel samples. This enables fuel professionals to predict microbe problems before they actually become problems.
Why Microbe Prevention Is Important for Critical Use Facilities
The potential consequences of microbial contamination speak both to the seriousness of microbe problems for critical users and the importance of knowing how to solve them when they occur. And they certainly speak to the importance of knowing the best practices for preventing these critical problems from manifesting themselves in the first place.
For these sectors, solving these problems is of an even more critical nature than for other people. Whether it’s local government, city utilities, or municipal works departments, data centers, utilities, health care, telecom….. their constituents all have the same expectations – 100% reliability and service provision at all times, especially during emergency situations when it’s most critical. Excuses won’t fly at those times. To meet these expectations, government entities rely on their emergency backup generator systems and their stored backup fuel to ensure 100% service at all times and in all situations. And that means they rely on their stored emergency fuel remaining microbe-free and problem-free.
Preventive Maintenance Recommendations for Stored Fuels
Given the importance of service reliability, prevention is always the best medicine. All of the common problems discussed above – instability, water levels, sludge formation, microbial contamination – they all have fuel maintenance recommendations to help combat them.
Preventing Microbial Contamination for Critical Use Fuels
Preventing microbe problems so the expectations of local constituents continue to be met centers two things: Monitoring levels of moisture in the storage tank and Tracking microbial contamination in the fuel and tank.
Check tanks for water levels at regular intervals. Microbes need free water to live and thrive, and water buildup is one of those inevitable things that’s virtually impossible to completely eliminate from a storage tank. Facility and fuels managers should ensure that monitoring water levels in their fuel storage tanks is part of their routine housekeeping protocols. Use water paste and a tank stick or sounding tape to detect the depth of water phase in the tank. It’s easy, quick, and can be done by just about anyone.
Once a detectable amount of water phase shows up during monitoring, remove as much as it as you can. Microbes don’t need much water at all to multiply to problematic levels within a short period of time. It is not uncommon to see microbe problems develop within just 3 months after a storage tank has been completely cleaned.
Pay attention to filter life and operational signs. As microbes grow in fuel and storage tanks, they produce
acids and biomass that destroy fuel quality and plug filters. Without being able to look in the tank and see what the actual fuel looks like, paying attention to how filters and equipment are performing on that fuel can give you a view as to how the fuel quality is. A change in filter change intervals or downgrade in engine performance can be a sign that something microbial is going on with the fuel.
Microbial monitoring is key. Microbial presence and fuel health is something that should be monitored on an ongoing basis, not just when you think a problem is arising. Better yet, regular monitoring of microbe levels in stored fuel can help government operations managers predict when a problem is getting ready to happen. Which means they can take quick action in real time. Next-generation ATP testing is the best practice test method to use for this essential function.
Testing and Monitoring For Fuel Instability
Fuel instability results from chemical chain reactions which start when the fuel is exposed to oxygen, water, light, certain metals, and acidic microbial byproduct compounds. These reactions result in fuel darkening, fuel stratification, and the buildup and fallout of fuel heavy end deposits.
Observe the color condition of fuel sampled from storage tank in question. Fuel that is darker than fresh diesel fuel is said to be “stratified” due to heavier components of the fuel becoming unstable and falling out of solution, changing the color of the fuel.
Note any change in frequency of filter plugging or replacement. Unstable fuel generates deposits that plug filters at greater frequency.
Note changes in black smoke and/or emissions from the engines using the fuel. Unstable fuel will result in higher black smoke levels or shortened DPF service intervals because the filter is filling up at a quicker pace. Black smoke is generated because the now-insoluble heavy end components of the diesel fuel do not burn completely, resulting in soot particles in the emissions.
In cases of greater importance/monetary value, send fuel samples away for ASTM testing. Bell Performance can facilitate state-of-the-art testing for both oxidative and stability testing using official ASTM protocols. This kind of testing typically costs several hundred dollars and is appropriate only for large-scale fuel users requiring legally-certified stability test results (such as for certain kinds of fuel certification). ASTM fuel testing legally confirms if the fuel in a storage tank meets legal stability standards.
Testing and Monitoring for Cetane Value
Low cetane value is strongly linked to subpar diesel engine performance in multiple areas – starting, combustion operation, emissions. Low cetane value is always relative to what the engine requires i.e. the same fuel (with a cetane rating of 45) could be adequate in one engine requiring 45 cetane but inadequate in another engine requiring 47 cetane. Confirmation of low fuel cetane value involves a combination of observation and testing.
Note changes in black smoke and/or emissions, as well as shortened DPF filter service intervals. Inadequate cetane value contributes to incomplete combustion and greater amounts of black smoke and soot particles in the emissions and DPF filter.
Note any observable changes in engine performance. Is the diesel engine harder than usual to start, especially in cold weather? Does it run more roughly than usual? A yes answer can indicate low cetane value. Proper cetane value contributes to easier starting of diesel engines, especially in cold weather.
In cases of greater importance/monetary value, send a fuel sample away for ASTM testing. You can have a Cetane Index test fairly inexpensively, and it fits into the official ASTM D975 standards for diesel fuel.
Testing and Monitoring for Tank Sludge
Tank sludge buildup is a phenomenon that takes place gradually within a storage tank. As we have noted, “sludge” is the common name for the heavy-end components of petroleum fuels that come out of solution in unstable fuel, dropping out and falling to the bottom of the tank. Excessive sludge presence in fuel tanks can be a sign of currently-unstable fuel and may also be a problem if portions of the sludge are carried by drawn fuel into the diesel engine.
Note changes in black smoke and/or emissions, as well as shortened DPF filter service intervals. Sludge particles in fuel will not combust fully, leading to greater black smoke emissions and premature filling of DPFs.
Observe color condition of fuel sampled from storage tank in question. Darkened fuel condition can be a sign of both currently-unstable fuel (correlated with sludge production) and the presence of existing sludge being drawn back into the fuel on its way out of the tank.
Note any change in frequency of filter plugging or replacement. The presence of tank sludge in fuel will plug fuel and tank filters at a greater interval than normal.
Fuel Storage Tank Maintenance Recommendations – Diesel Tanks
If the fuel is tested and it fails one or more of these essential measures, it’s time to consider a solution.
In the absence of defined testing, if you notice changes in the way your equipment runs, that also signals that it’s time to look more closely at solutions. And if you have a positive microbe test, then you REALLY need to take action. But what action is the best to take?
Remember, some people, like fuel polishers, insist that mechanical solutions, like filtering and polishing, are the only way to go. For them, fuel polishing will do anything – some have even claimed they can “polish” sulfur right out of diesel fuel. Other parties – we’ll call them ‘additive makers’ – want you to believe anything and everything can be solved by some magic potion you add to the fuel. They advocate for a chemical solution only for whatever problem they see. To them, chemicals will solve everything.
The truth lies in between (or even outside) of their ways of thinking. The truth is that the best practices include all of these, plus testing, too.
Fuel PM: The “What To Do” Guide For Fuel Problems
If you have this: |
Poor cetane rating |
Do this: |
Chemical solution – Add cetane improver to the fuel. |
If you have this: |
Microbial growth in fuel or tank |
Do this: |
Hybrid solution – Add biocide, circulate fuel mechanically to ensure complete kill. |
If you have this: |
Excessive water & sediment |
Do this: |
Hybrid solution – Pump out water, mop up remnants with chemical water absorber. Filter or polish out sediment to clean the fuel. Add fuel stabilizer and biocide at the end. |
If you have this: |
Out-of-spec distillation reading |
Do this: |
Mechanical solution – Get rid of the fuel (it may be contaminated) |
If you have this: |
Sludge in the storage tank |
Do this: |
Hybrid solution – Use chemical sludge dispersant, followed by polishing to clean the tank. |
If you have this: |
Darkened or stratified fuel |
Do this: |
Hybrid solution – Fuel polishing to remove solids, followed by treatment with stabilizers and biocide to protect fuel quality in storage. |
As you can see, when it comes to fixing and/or preventing fuel problems through fuel maintenance, the best practice solution is often not to one or the other – chemical solutions vs. mechanical solutions. The real truth is somewhere in the middle. Some problems respond very well to chemical treatment while other problems can only be solved by a mechanical fix. And there are other problems that need the hybrid approach – a combination of both chemical and mechanical solutions that work synergistically with each other to produce the best results.
Chemical Problem-Solving Treatments
“Chemical practices” center on adding effective chemical treatments to the stored fuel to either fix an existing problem or prevent a possible future problem from developing. The important chemical treatments to consider are fuel stabilizers, water controllers, biocides and sludge dispersants.
Fuel stabilizers are typically antioxidant packages that prevent the chemical reactions from starting that cause fuel quality to break down over time. Oxidative chemical reactions in diesel fuel are a chain reaction; this means that the process is started with a few chemical reactions that lead to more chemical reactions, eventually leading to widespread breakdown of that diesel fuel. Oxidative fuel stability ingredients, like Bell Performance’s Dee-Zol Life, function by stopping these first chemical reactions in the process. If you stop the first chemical reactions in the chain reaction, you stop the rest of the chain reaction and, in this case, this means preserving the fuel quality of the stored diesel fuel.
Keep in mind that these are called stabilizer packages for a reason. The best fuel stabilizers are combinations of active ingredients necessary to target the multiple avenues that lead to degradation of fuel stability. They should contain the aforementioned antioxidants, they should contain dispersants (to keep sludge particles suspended in fuel), metal deactivators (to combat the effects of catalytic metals) and antiperoxidals (to combat the effects of peroxides in fuel).
Water Controllers
Water control ingredients are essential to control the buildup of water that happens in stored diesel fuel and stored ethanol fuels. Bell Performance manufactures a number of single function and multifunction fuel treatment products (DFS Plus and Ethanol Defense) that absorb water buildup in both ethanol and diesel fuels.
When considering the need for water control chemicals, it’s important to recognize that they have limitations. They aren’t designed to get rid of huge amounts of water in fuel. And this fact confirms the need to consider a multi-prong approach when trying to solve fuel problems that involve water presence in storage tanks.
Demulsifiers
Similar to water dispersants and absorbers, demulsifiers can be a useful tool to combat water in storage tanks; specifically, difficult-to-remove water that has turned into a fuel-water emulsion. These emulsions can be really difficult to resolve without the help of a chemical demulsifier. Demulsifiers like Demulsifier EB and Bell Tank Treatment EB work to break the bonds holding water microdroplets into stored fuel. The droplets coalesce and aggregated and fall out into a free water phase that can be easily removed.
Proper application to especially important for demulsifiers. This is because if one is not careful, it can be possible to re-emulsify the separated water back into the fuel. Typical application instructions would be to add a demulsifier and circulate the fuel at a moderate level (heavy circulation can recombine the water and fuel). Then the important step is to allow time for the water to separate out before proceeding with further action steps like mechanical processing.
Sludge and Biomass Dispersants
Sludge and biomass dispersants (like Bell Tank Treatment SDF) have recently come to the forefront of best practices because they can keep stored fuel tanks clean of problematic sludge buildup while also dispersing microbial biomass formations. This enables the storage tanks to stay cleaner while enhancing the effectiveness of any biocide that is used.
The recommendations for best administrations of these fall in line with similar recommendations for other chemicals. They work best when in contact with the fuel. Which means it would be important to circulate the fuel after adding the chemical.
Biocides
Biocides are essential weapons in the fuel manager’s arsenal for making sure that stored fuels stay free from bacterial infestation and the headaches that these infestations cause. Bell Performance Bellicide is a dual phase biocide that works in both the petroleum and the water phases of stored fuel, including gasoline, ethanol, diesel and biodiesel. Bell Performance ClearKill also offers the same great benefits as Bellicide, while also supplying corrosion proteciton for tanks and not contributing any sulfur to sensitive stored diesel fuels.
Given the choices out there for biocides, it’s important to know what makes a good biocide vs. a not-so-good one. The best biocides should incorporate the following characteristics
- Broad spectrum
- Fast acting
- Long lasting kill rate (all biocides get used up. No biocide lasts forever. 30-60 days is the industry best)
- Dual-phase (Water and fuel) effectiveness (some chemistries like Biobor are not effective in water)
- Must be registered with the EPA Pesticide division (if they don’t have an EPA registration number, they aren’t registered and it may be illegal to use it in your particular state)
Chemical Treatment of Microbe Problems With Biocide
There are best practice solutions available today that make solving microbe problems in government & municipal stored fuels a much easier proposition than in the past. They’re not hard, they just have to be implemented.
Remove the water. Checking for water was an essential first step. Now it has to be removed. Most tanks have the ability to drain off water without unduly disturbing the stored fuel phase. If yours does not, contract with a fuel service provider to pump off as much of the water as possible. The best providers will also utilize water scavenging chemical treatments to effectively get what water they cannot drain off mechanically. It’s important to get as much of the water out of the tank as possible. And if the tank contains a fuel-water emulsion, they’ll need to use a demulsifier to break that and allow the water to separate.
Use biocides to kill the microbes. There is no way to get rid of a microbe problem without using a biocide to kill the microbes. Some water treatments imply they can solve microbe problems by removing water, but this isshort-sighted and dishonest. Living microbes can only be eliminated by killing them through administration of a biocide to the fuel.
Use biomass dispersants in conjunction with biocides. Many times, the living microbes in the storage tank will have produced significant amounts of biomass (biological secretions) that, in themselves, will plug filters, but that will also shield microbes from biocide action and prevent a complete microbe kill. If there is evidence of substantial biomass presence in the fuel or sticking to the surfaces of the tank, a government fuel manager should administer a biomass dispersant treatment alongside the biocide. This will break up and disperse the biomass and allow for a more full and effective microbial kill by the biocide.
Test…test…test for microbes. Both before and after. It’s not enough to simply apply biocide and hope for the best. Given what’s riding on the health of their fuel, government facility/operations fuel managers should do simple microbial testing, both before and after treatment, to ensure the problem is resolved.
A second generation ATP test is a simple in-field test that’s cost-effective and gives a specific microbe count for the fuel sample tested. ATP testing should be conducted on both a fuel sample (taken about 18 inches from the tank bottom) and a water bottom sample from the stored fuel tank. These should be done before and after treatment.
If the after test shows a significant microbe presence still remaining, that can usually be fixed by a second application of biocide.
Remember, microbial presence in a stored fuel tank environment is a complex biome, almost an ecosystem of sorts for microbes. One size treatment does not always fit all. Use ATP microbial testing to confirm the problem is eradicated, for peace of mind. This is the best chance for government and municipal stored fuel users to ensure microbe problems don’t cost them or their constituents.
These are the best practice recommendations for ensuring the greatest chance of problem-free operation for the stored fuel used by governments & municipalities.
Limitations of Chemical Treatments to Protect Stored Fuels
All this having been said, chemical “fuel additives” cannot do everything, despite what fuel additive companies tell you. The most relevant limitations that should be considered are:
- Water controllers can effectively control limited amounts of water but are not designed to make large amounts of water disappear.
- Fuel stabilizers need to be added when the fuel is fresh, before signs of instability become apparent. Once fuel sludge has developed in a fuel and its storage tank, a stabilizer will not put it back together again.
Now that the limitations of chemical fuel additives (they can’t do everything) has been brought to light, we consider that mechanical fuel treatment processes have a great deal of value in filling in the gaps to protect stored fuel quality. “Mechanical processes” is another name for fuel polishing.
Mechanical Fuel Processing
A good mechanical process will involve the use of filters and water separators to mechanically remove particulates and water from the fuel and its storage tank. Mechanical filtration is very useful for taking fuel that is out-of-spec and bringing it back into specification – a great advantage for facilities that are legally required to keep their backup fuel ready for emergency use. Mechanical processes are also the best way to handle the sizable amounts of water that many fuel storage tanks accumulate over time if they are not diligently watched.
Fuel filtration systems in vehicles/engines
Filtration to remove contaminants has long been known to an important part of preventing problems. The need for filtration of diesel fuels goes all the way back in the 1930s or before, with a 1931 Caterpillar owner’s manual stating that 90% of diesel problems were due to dirt or water in diesel fuel.
Today’s high-tech engines simply couldn’t survive without effective fuel filtration. On modern engines, this generally consists of 2 sequentially-placed filters – a primary filter and a secondary filter. The primary filter usually has efficiency ratings from 7 µ to 25 µ. The secondary fuel filters are placed between the transfer and high-pressure injection pump to protect the high-pressure fuel pump and sensitive fuel injection components from particles that can cause wear damage. Typical ratings for secondary filters in high-pressure common rail fuel systems are in the 4 to 5 µ efficiency range.
The relevance of all of this comes into focus when we consider how the tolerances of modern diesel engines have changed. Now, engine manufacturers have specifying ISO fuel cleanliness counts that are 1000x times better between the fuel pump and the injector system.
Typical fuel cleanliness levels are ISO rated at 22/21/18, which means a particle count of 20,000 – 40,000 per ml for particles of 4 microns or higher, 10,000 – 20,000 per ml for particles of 6 micron or higher, and 1,300 – 2,500 per ml for particles of 14 micron or higher. Indeed, particles significantly smaller than 4 µ in size are now potential wear contributors to important parts.
This has important implications for fuel maintenance. When you have stored fuel being used in high-tech diesel engines that have such low tolerance for particulate contamination, it becomes imperative to try to ensure these issues don’t develop. As well as being imperative that good mechanical fuel filtration become a part of the fuel’s upkeep.
Different Options for Mechanical Processing
Any discussion of mechanical processing for stored fuel means, at a minimum, fuel filtration. As you may imply from above, there are filters to remove particulate and organic contamination, and there are also filters to remove water contamination.
Water is generally removed from fuel using a stripping or coalescing mechanism. A coalescing filter separates water by allowing it to pass into the media where droplets are captured and combined to form larger droplets which are finally released on the downstream side. As water droplets in low interfacial tension fuels form stable emulsions, both strippers and coalescers can become ineffective and cannot achieve required water filtration efficiency.
How Effective Is a Filter? Filter Beta Ratings
In terms of particle filtration efficiency, beta ratio is still a quantitatively way to define filter medium effectiveness to keep diesel fuel relatively free of damaging aware particles. Beta ratios are defined as the ratio of the number of particles upstream to the number particles downstream at a specific particle size. Beta ratios unfortunately are often inadequate measures of fuel filter performance, being derived from standardized multi-pass fuel filter tests while on-vehicle filtration generally happens in one single pass.
Mechanical Processes for Stored Fuel Have Their Limitations, Too
The biggest limitations that fuel filtration and similar processes have in protecting stored fuel quality are that they do nothing to keep fuel problems from coming back. Fuel polishing removes from the fuel what’s not supposed to be there. If you manage stored fuel of some type, you may even have had this scenario play out where you are. You engage the services of a fuel polisher, who may come out and do an admirable job of cleaning up darkened fuel and turning it clean and bright, just as it supposed to be. Yet, once the mechanical process is concluded, there’s nothing to stop the fuel from darkening again. Or developing a repeat microbe problem within a couple months. Mechanical fuel processing addresses current problems, it does not prevent future ones.
The Hybrid Approach to Fuel PM Addresses Both Issues
Given the limitations of either side, the best practice recommendation for protecting stored fuel is to use a combination of both methods. The best practice is to start with the use of periodic mechanical fuel and tank servicing to clean up and remove existing water, sludge, asphaltene dropout and microbial growth. This is combined with the addition of quality chemical fuel treatments that both enhance the effectiveness of fuel polishing (water controllers to scavenge leftover water, sludge dispersants to remove hard-to-reach asphaltene collections) and prevent these problems from returning (biocides, fuel stabilizers) for long periods of time than would be possible without their use.
How does your Fuel PM stack up?
Maybe you already have some kind of fuel preventive maintenance program in place. How does it stack up to the best practices recommended? Try this quiz and assess how many of these statements are true for you.
Your filter-change interval suddenly shortens or changes |
5 points |
You notice a change in the normal performance of vehicles, engines or generators that use your stored fuel, especially with respect to any of the following:
|
4 points |
You’ve stored fuel for more than a year without having its specifications test-confirmed |
2 points |
You have an underground fuel tank that collects water in the spill bucket which isn’t emptied regularly |
2 points |
You don’t know or don’t remember how old all of the fuel in your storage tank is |
1 point |
You have stored backup fuel that isn’t checked on at least a monthly basis |
1 point |
You’re not required by law in your industry to test stored fuel properties |
1 point |
You recently switched fuel providers |
1 point |
You don’t know who to call if you had a sudden problem that you suspect could be fuel-related |
1 point |
You don’t not currently have a preventive maintenance program for your stored fuel |
2 points |
Now add up your applicable number of points.
Zero points: |
You are most definitely “fuel-ready”. Good job! |
1-2 points: |
There are some areas of moderate concern that you’ll want to look more closely at. Especially if you don’t monitor your stored fuel quality on a regular basis. |
3-4 points: |
You’re not in deep trouble yet, but the potential for fue contamination problems is getting larger. You may want to consider some proactive action. |
5 points or more: |
You’re at greatest risk for fuel contamination problems, if you don’t already have them. Either way, you’ll want to seek out a partner who can help. |
“Fuel PM” When Things Are Quiet
When it comes to fuels, a lot of the success that you’ll have in implementing the above steps relies on groundwork you can lay during the “times of plenty” – when everything is fine and no storm is on the horizon. The best thing you can do on an ongoing basis is control the water buildup in your storage system and keep the microbes at bay. You likely have water remediation steps you take regularly, but what about the microbes?
Microbial growth in fuel tanks definitely falls under the category of “better safe than sorry”. It’s much less stressful (and much less expensive) to prevent microbial growth in fuel tanks than to try eradicate an active infestation after it’s established. Especially when the infestation spreads to all areas of your fueling system.
Beyond proper water control steps like draining, the best thing you can do to prevent microbial growth is to periodically treat your tank system with a biocide. Once a quarter is a good interval, though if your housekeeping measures aren’t the greatest, it’s in your best interests to do it sooner, say every 2 month or 6 weeks.
Biocide treatment is an irreplaceable step if you have any hope to keeping microbial fuel problems at bay. Even mechanical fuel polishing and tank cleaning are not enough by themselves – it is an industry standard expectation that you can go from a completely clean tank to signs of microbial activity and corrosion damage in as little as two months. And that’s starting from a completely clean tank, too.
Biocides are highly regulated and very concentrated – a typical maintenance treat rate would only be 1:10,000, meaning you could treat a 5,000 gallon fuel storage system with only half a gallon of biocide. Such a low treat rate makes maintenance treatment very cost effective – you might only pay $100-$150 at the most to ensure that a 5,000 gallon fuel system stays problem free.
If you want to ensure the best chance of success with your fuels in the quiet times when there’s no storm expectation, periodic treatment with a biocide is your best protection.
ATP Microbial Monitoring to Predict Problems
Speaking of “best chance of success in the quiet times”, we’ve mentioned the concept of ATP testing of stored fuels to monitor microbe levels. We’re rapidly approaching the point where more and more fuel managers are seeing the value of monitoring the microbe levels in their stored fuel tanks. If you do ATP testing monthly, you build up a seasonal picture of what’s going on in your storage tank. When microbe levels rise above a certain level, you can make real time decisions to prevent problems that WILL happen if you don’t do anything.
That’s perhaps the biggest difference between sound fuel preventive maintenance and the traditional, reactive way of doing things. We have better tools, like ATP testing, that allow us to stay on top of issue where they become issues. Before critical systems fail during hurricanes. Before microbes destroy emergency backup fuel quality.
ATP microbial monitoring can be done on-site or on fuel samples submitted to groups like Bell Performance (who have fuel sample submission kits that provide everything you need to package and ship fuel samples). The ATP tests themselves only take a few minutes and give a measurement of the actual number of microbes in fuel and water samples.
The Best Practices of Fuel Maintenance – Do You Have What It Takes?
We know that the diesel fuel that Fleet and Facility Managers and so many others rely on has changed dramatically in recent years. Maintaining fuel quality is more demanding and involved than it used to be. New problems and solutions have evolved and forward-thinking professionals now know that they must adopt a fuel-specific preventative maintenance program.
We understand that everyone is being tasked to do more with less. There are lots of different options to consider and getting it right is the only option. After all, it could be a matter of life and death!
For those who aren’t confident they can cover all the bases by themselves, Bell Performance offers the Bell Fuel and Tank Services program, a turnkey program utilizing best-of-breed chemical and mechanical technologies for fuel and tank maintenance. We can help implement a self-managed program or offer a fully out-sourced PM solution. We offer provide peace of mind against equipment damage, engine failure and general liability, and deliver the most cost-effective approach, including an exclusive guarantee that your fuel remains in clean, stable and working condition.
Fuel Preventive Maintenance Programs & Taking Advantage of Partnerships
All of these afore-mentioned best practices are also essential aspects of fuel preventive maintenance programs that are recommended for anyone with a substantial stake in ensuring their stored fuel quality is protected. But many of the entities that need to do this the most find themselves with neither the time nor the human capital resources (personnel) to effectively implement such an important program. If you find yourself in that boat, it would be a good idea to partner with a fuel & tank services company who can bring all of these best practice recommendations under your umbrella. These partners will typically handle all of the testing, assessment, remediation and preventive treatment of your stored fuels and storage tanks. And some of them will also provide certain guarantees on the on-going condition of your stored fuel that’s under their care.
Engaging the expertise of a fuel & tank services partner may be something to consider if you need to know your stored fuel is protected for future use but you feel you may be lacking in the time and money needed to properly ensure this. If this sounds like you, Bell Fuel & Tank Services provides these essential fuel PM elements that may be worth your consideration.
You can trust Bell Fuel and Tank Services to ensure that you’re Fuel-Ready!
Helpful Resources
Fuel Changes and How They Affect You
Webinar
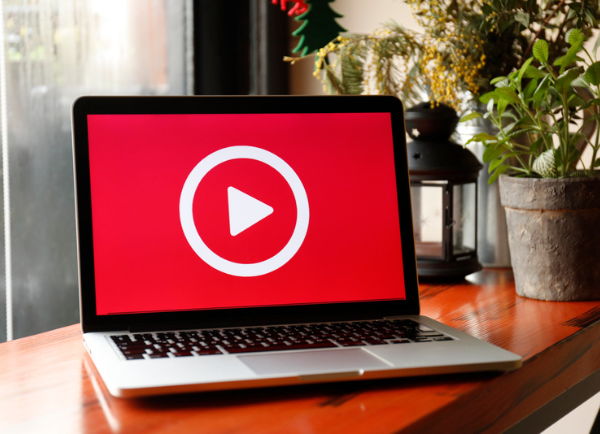
What's My Fuel Health Score?
Webinar
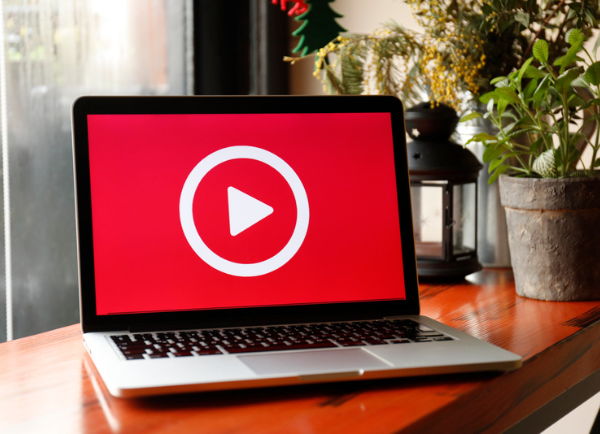
Four Essentials To Know About Fuel & Three Solutions
ebook
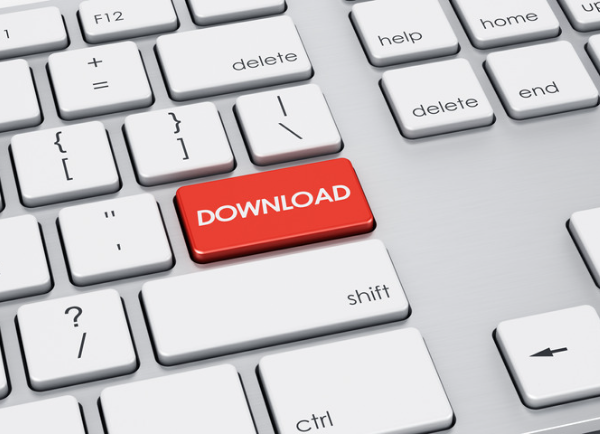
Top Ways Microbes Cause Fuel Headaches
ebook
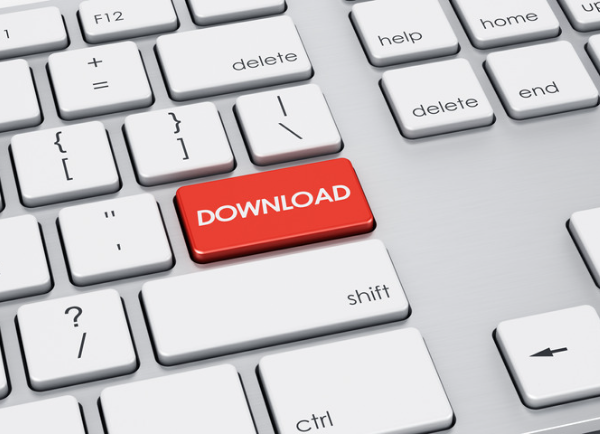
The Fuel Additive Buying Guide
ebook
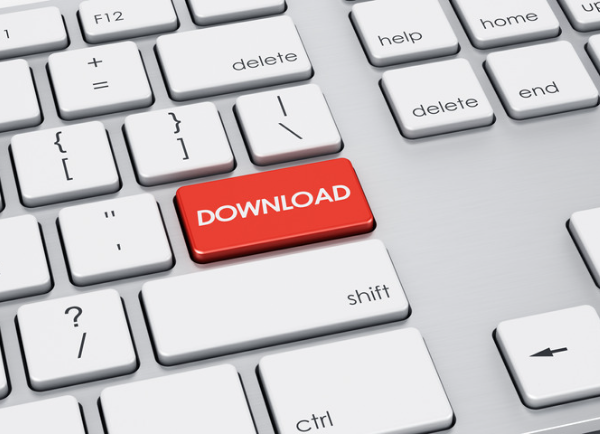
Fuel Health Checklist
Checklist
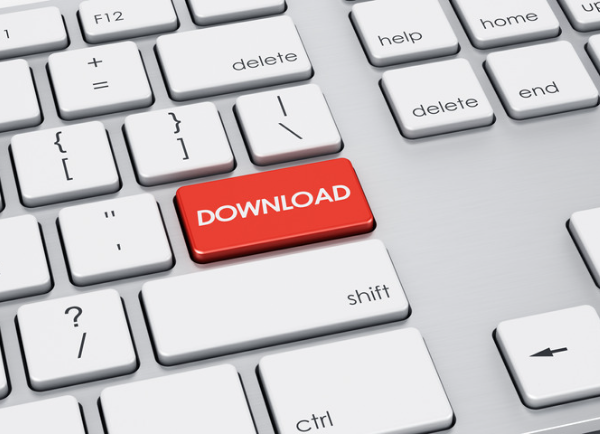
Essential Fuel Tests
ebook
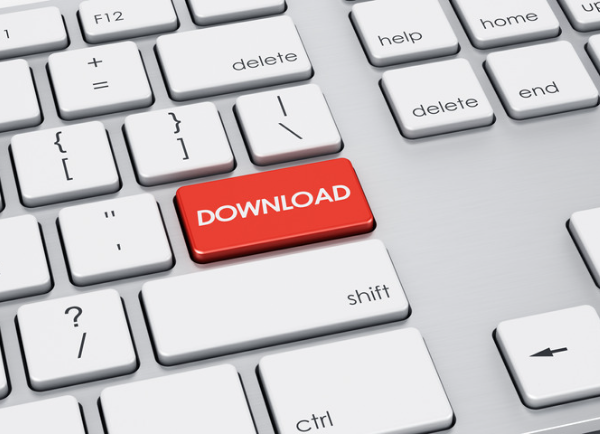
How to prevent diesel fuel microbes
ebook
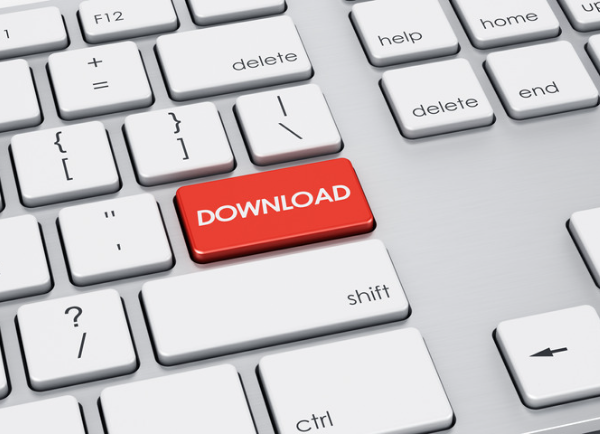
Fuel Tests You Need To Know About
Webinar
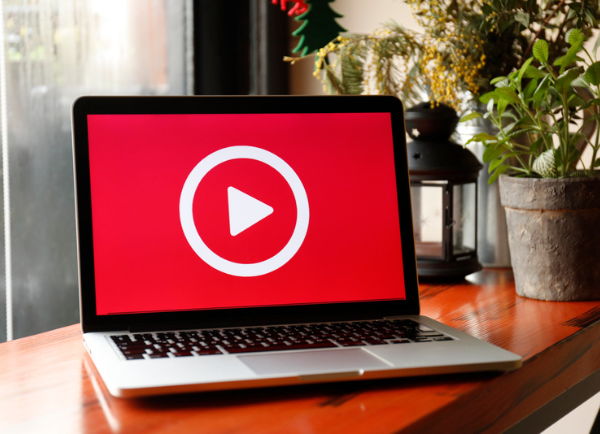
Fuel Storage on our Commercial Blog
4 min read
What Hospital Fuel Polishers Should Know About Fuel Additives
Jun 10, 2025 by Erik Bjornstad
3 min read
Keeping Your Fleet Fuel-Ready: A Practical Health Checklist for Fleet Managers
Jun 3, 2025 by Erik Bjornstad